Prefab Homes Guide Pt.1: Where to start?
With the appeal of affordability, efficiency and sustainability, the popularity of prefab homes in Australia is certainly on the up.
If you’re thinking of going prefab, at first glance the process can seem pretty simple: choose a design, order it, deliver it and move in. And while it is a relatively simple process compared to custom homes, there is of course, a bit more to it.
To provide more definition to the prefab process, we’ve put together this guide that is designed to walk you through each step of the prefab process and give you a greater picture of the considerations.
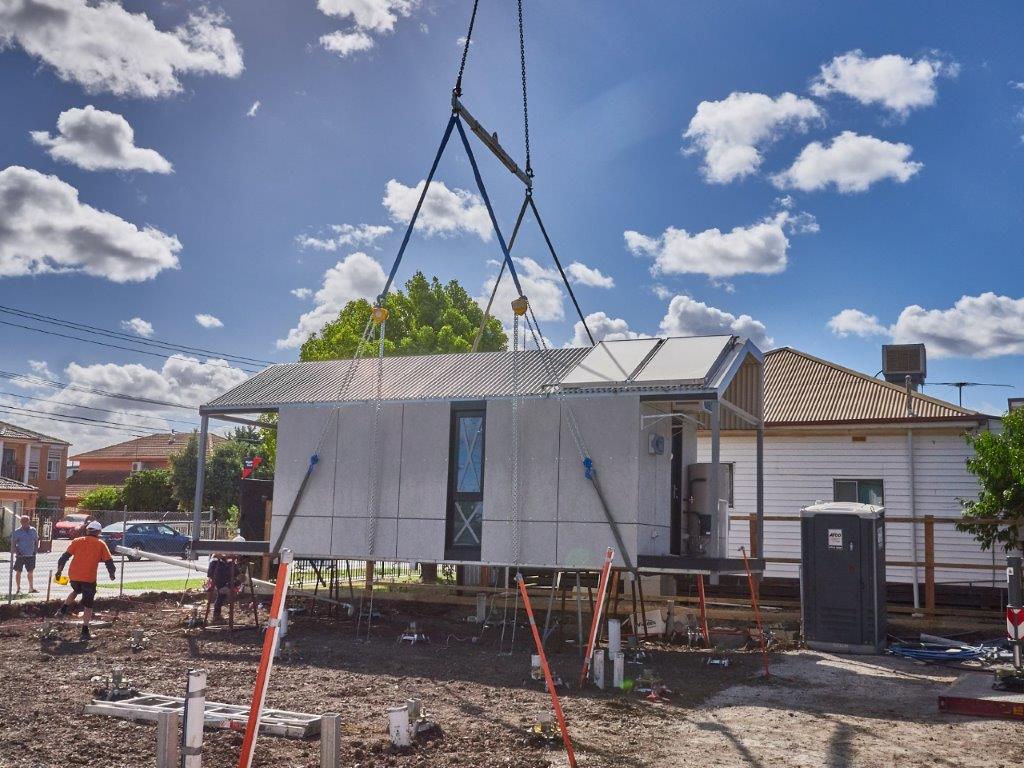
A prefab house being craned in. Photo courtesy of Launch Housing.
What’s Prefab?
If you’ve already started your research, you would’ve come across terms like ‘modular’, ‘3D’, ‘factory made’ and ‘panelised’. You’re probably wondering what the difference is.
Prefab – short for prefabricated – is the umbrella term used for any structure that’s created offsite and assembled and installed onsite. The term covers a range of different systems, processes and services which we’ll cover throughout this guide.
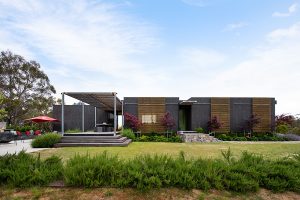
The ‘Mod House’ suits all environments from country and beach blocks through to inner-city sites. Built by Prebuilt Australia.
Where did Prefab come from?
The concept of prefab can be traced back to Roman days when prefabricated fort sections were mass produced and delivered to distant locations. Across Europe, prefabricated building approaches helped address housing shortages during the postwar era.
During Australia’s gold rush, prefab dwellings helped solved Melbourne’s housing and skilled labour shortages, with thousands of flat-packed cottages imported to keep up with the boom.
Though not a new concept, prefab homes have come a long way to offering affordable architectural design to a modern consumer. Far from the stigma of cookie cutter designs and cheap builds, leading prefab companies employ design thinking to create homes that are architecturally beautiful, respond to current sustainability concerns, and offer a real alternative to traditional construction.
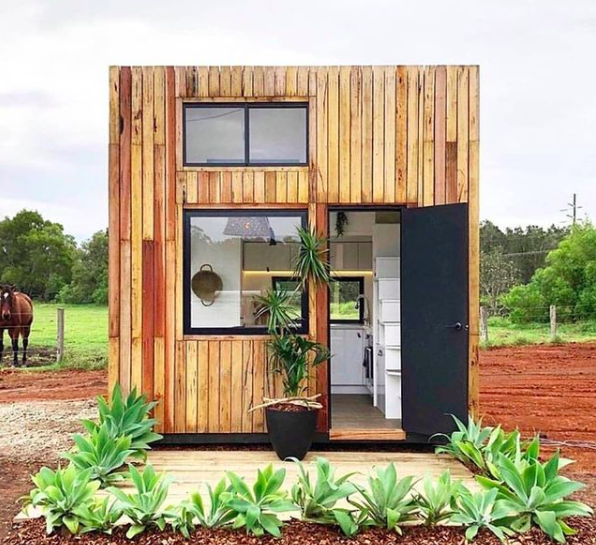
A popular choice is the container home. Photo courtesy of @container.house.
There are different types of prefabricated systems, the most common of which we’ll cover below.
Modular housing systems
Modular or 3D systems are prefabricated structures comprising multiple 3 dimensional sections (i.e. modules) that are constructed off-site and assembled at the final site. Most modular builds will be near complete when they arrive on site – with walls, floor, ceiling, wiring, plumbing and interior fixtures and fittings.
Modular systems can be used to extend an existing home, or to create an entire home. Like LEGO blocks, modules can be placed side-by-side, end-to-end or stacked, allowing a variety of configurations and styles.
Within the modular system, the word ‘pods’ refers to non-structural modules such as bathroom or kitchens that are installed within the building.
Most modular home providers will have models that can be purchased as is, or customised to suit individual requirements – with a further range of options for the facade, cladding, internal fittings and colour selections.
Some key advantages of Modular systems
- Quick build times – typically 14-16 weeks off site.
- Modules can be manufactured concurrently with on site works (such as site preparation) and arrive nearly finished.
- Individual modules can be combined, to create larger spaces and multi-level structures.
- Minimised on-site waste and reduced impact on the land.
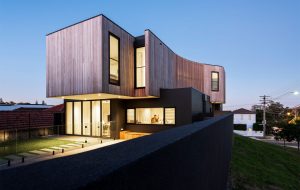
Built using prefabricated modules and installed in 1 day by Prebuilt Australia. Photo by @tfadtomferguson.
Panelised housing systems
Panelised or 2D systems – also referred to as precut, flatpack or kit homes – are pre-cut, pre-sized, and pre-shaped elements that are partially built off site and then delivered on site for assembly and construction.
Unlike modular systems, they’ll arrive on site as 2-dimensional flat-packed panels, making them easy to transport and customise. The panels can be made from various materials including concrete slabs, timber or hybrid-timber.
When talking about 2D panel homes, you’ll hear the terms ‘open-panel system’, ‘closed-panel system’ and ‘enhanced panels’.
Open panels are non-insulated and leave a lot more construction work to be done on location, whereas closed systems come with insulated walls. Enhanced panels mean things like windows and doors, services (electrical or plumbing) or finishes such as external cladding or internal lining have been added to the panel.
Some key advantages of Panelised housing systems
- Cheaper and easier to transport.
- Higher level of customisation and configuration options.
- Quick to assemble with limited labour requirements.
Innovations in prefab technology
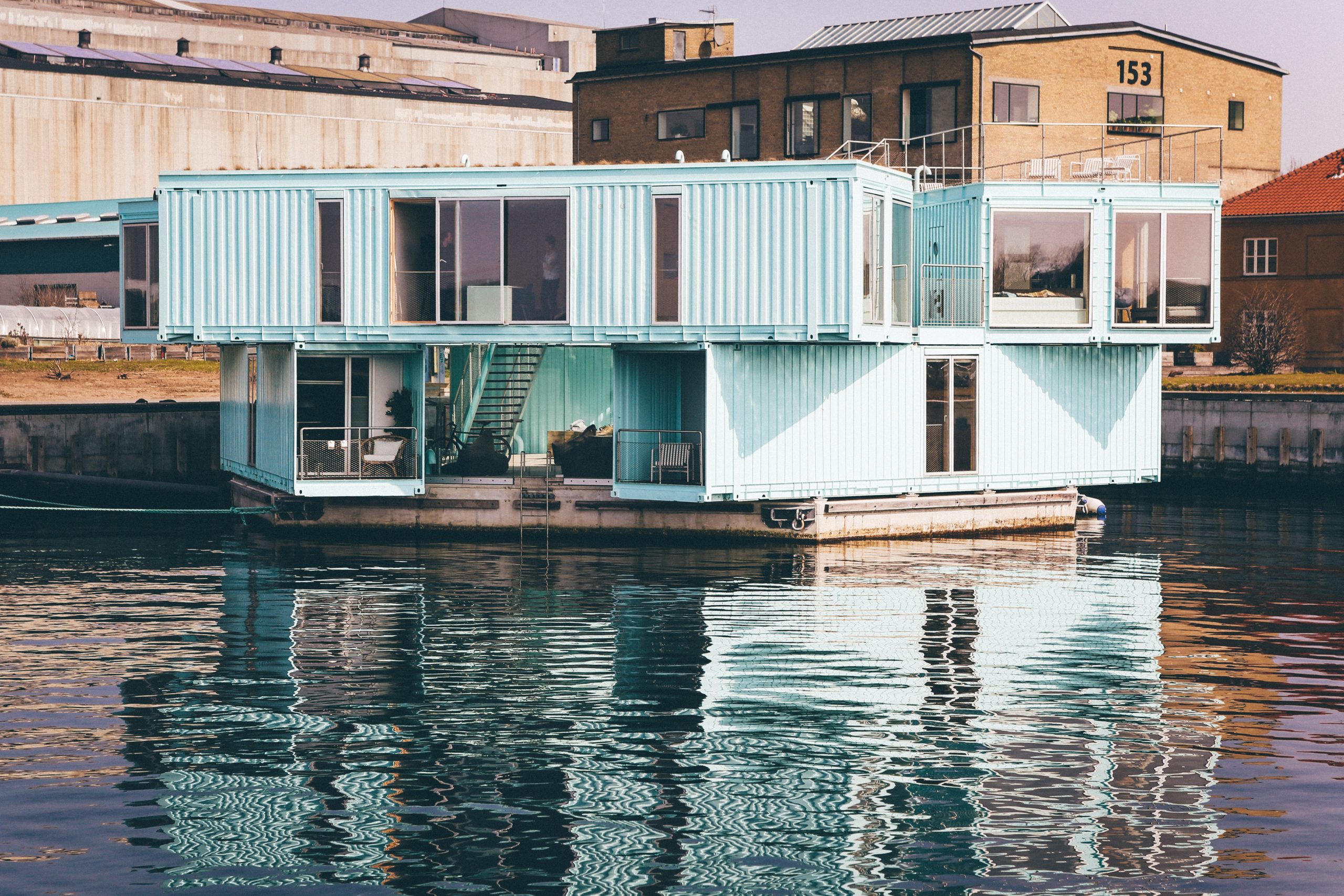
Prefab on the water. Photo by Nick Karvounis on Unsplash
Today, leaders in prefab construction embrace innovation as they strive for a better built environment – with high quality and efficient building solutions. The innovations in modern prefab offerings aren’t limited to cost savings, but about offering a better quality product. Some key innovations include:
1. Reduced time frames and labour costs
As the prefab fabrication process happens in a factory, the site can be prepped in tandem – reducing the overall construction period and the labour costs along with it. PrefabNZ reports that construction time is shaved by a whopping 60% through offsite construction.
2. Increased safety for workers
The health and safety of construction workers is easier to manage in a factory setting than on a traditional construction site, with much of the work able to be conducted at waist height.
3. Lower environmental impact
The off-site fabrication process means less disturbance to the site and a low-impact construction process. Fabrication technologies designed to output an exact fit also mean less material and construction waste – which is a big deal considering that approximately 6.7 million tonnes of construction waste out of the total 20.4 million tons of waste the industry generated went to landfill in 2017.
4. Consistent quality and consumer confidence
The controlled manufacturing environment of prefab construction – where the weather isn’t an issue and machinery is used for precision – means that the output can be of a predetermined, uniform quality. Prefab homes also have to withstand transport loads, meaning they’re designed with extra considerations for durability. Further, with construction protected from the elements, there’s fewer delays and greater cost certainty for the customer.
Now you that you know that basics, learn everything about where to prefab in pt.2 of our guide.
Cover image by @Picturefilmstudio